ダイカストの鋳造波形から鋳造条件をAIがスコアリング
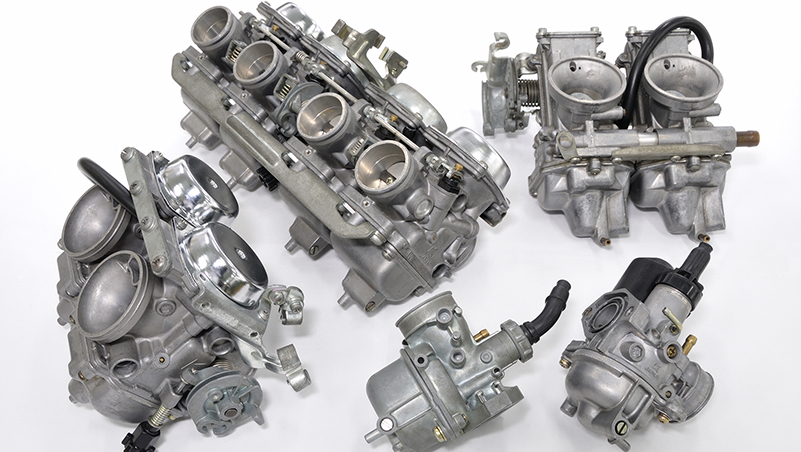
ダイカストの鋳造波形から鋳造条件をAIがスコアリング
ダイカスト工程の鋳造波形から、鋳造条件をスコアリングするAIを作成しました。自動算出された点数から、人が鋳造条件の正常・異常を判断するワークフローを構築します。
従来フローでは、熟練の検査員が射出(ショット)ごとに変位、圧力、速度などの測定値を示す大量の波形データを目視採点し、鋳造条件の正常・異常を判断していました。しかし、数十種類もの異常パターンを把握して波形データを読み取れる熟練者が年々減少しており、その技術継承が課題となっていました。
また、鋳造条件の確認は製造の後工程で行われていましたが、AI化により射出時に即座に鋳造条件が点数化されます。異常発生のフィードバックが早まることで、さらなる欠陥品製造を防ぐことが期待されます。
[ プロジェクトのポイント ]
- 鋳造波形データの読み取りをAI化し、鋳造条件をスコアリングする
- AIが不良品予測し、人間が正常・異常を判断する(共存)
- AI化によりドメイン知識を技術継承
提示された課題
- ダイカスト工程において、熟練の検査員が数十種類もの異常パターンを把握し、大量の波形データを目視確認していた
- 変位、圧力、速度などの測定値を示す鋳造波形から、鋳造条件の良し悪しを採点できるような熟練技術者が減少している
- 製造の後工程にて、鋳造条件を評価していた
問題解決までのアプローチ
本プロジェクトは大きく3つのフェーズに分けられます。現在までにフェーズ2まで進行しました。
1.優先的にAI化するフローを選択
プロジェクトを段階的に進めるために、数十種類ある異常パターンからテーマを数種に絞り、評価基準を設定しました。
2.スコアリングするAIを作成
鋳造波形と採点ルールを学習データとして、スコアリングするAIモデルを作成しました。このとき、学習用の波形データを準備するとともに、採点ルールを明確化します。
・インプット(説明変数) :変位、圧力、速度などの測定値(鋳造波形)、採点ルール
・アウトプット(目的変数):鋳造条件ごとの採点結果
3.実運用に向けた調整
実運用にむけたAIの精度向上に取り組むとともに、現場実装に向けてシステム構築を含めた最終調整を行ないます。本事例では、社内クラウドシステムに組み込む形式で提供予定です。
AI導入にあたってのポイント
ドメイン知識の継承
鋳造波形の採点箇所を決める際には、従来フローで使用している採点ルールを反映します。どこに着目すれば鋳造条件の正常・異常判断ができるかというお客様の現場に蓄積されたドメイン知識が活かされます。技術継承とともにAI化によって属人化を防ぎます。
スコアリング
OK・NGという正誤判定ではなく、結果を点数化することで段階的な評価ができます。はじめから完全な省人化を目指すのではなく、例えば、60点以下の場合のみ人間が目視チェックするといった運用フローを構築します。
[ プロジェクト概要 ]
クライアント名 自動車メーカー様
プロジェクト開始時期 2019年11月
[ 関連リンク ]
AIカスタマイズソリューション
https://skydisc.jp/solution/