生産計画DXだけじゃない、ミツワケミカルが考えるDXとは?
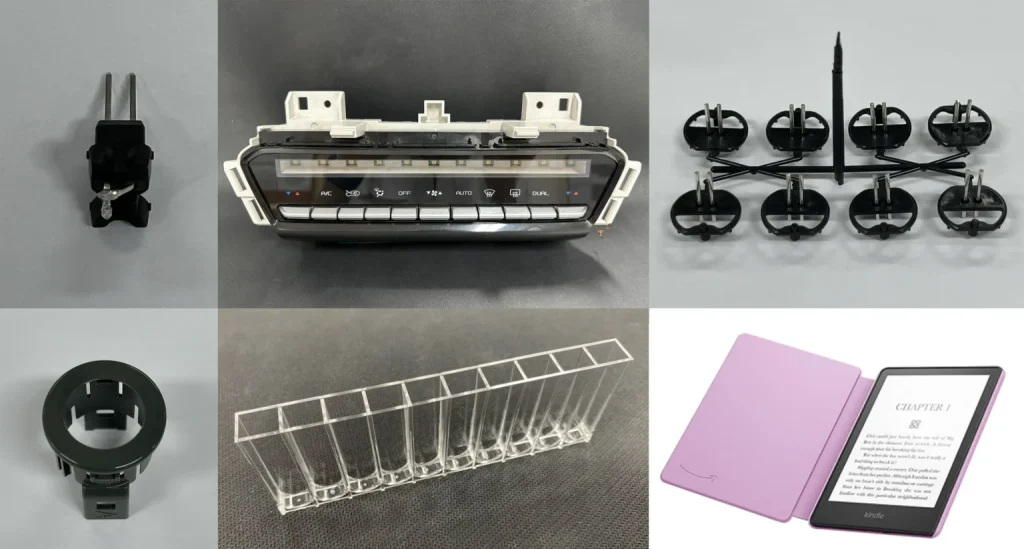
株式会社ミツワケミカルは、昨年に60周年を迎えたプラスチック成形の企業です。自動車関連事業を中心に展開しており、生産拠点としてタイ・フィリピンの2工場を構えます。 海外拠点を前提に業界に先駆けてクラウド利用を進められ、現在では業務の大半をSaaSで運用しています。そんな中、2023年6月より生産計画業務に最適ワークスを導入しました。 生産計画DXをはじめとしたDXを積極的に推進する理由を、ミツワケミカル代表取締役社長の神保様にお話を伺いました。 (最適ワークス導入の背景については、こちらをご覧ください)
株式会社ミツワケミカルについて
1962年、神奈川県にプラスチックの一貫生産メーカーとして創立して以来、プラスチックの多様化・高度化に併せ、精密金型製作から二次加工 (塗装・印刷・レーザーマーカー・組立等) まで一貫して開発・生産可能なメーカーとして発展。 1994年7月には、フィリピンマニラ郊外に一貫生産工場を現地法人として設立し、2007年4月にはタイバンコク郊外にも生産拠点を設置。グローバル化を積極的に推進してきた。
DXの着手は海外での事業展開に必須だった
2010年以降、日本での需要が減ってからも、海外に拠点のある日系企業に販売していくために、日本はマザー工場として維持していました。しかし、現地でスピーディーに開発~生産を行う目的や、輸送コストや人材確保の問題から、2018年に機械や倉庫を全て海外拠点に移設し、日本は営業拠点として運営することになりました。これにより、工場と取引先の物理的な距離が近づき、広い視点では業務効率の向上に繋がりました。しかし、工場の運営は非効率なままで、無駄な作業や設備稼働率の低さ、生産量のミスなどが目立ちました。これを受けて、グループ全体の業務を標準化し効率化することが必要だと思い、DXを推進してきました。
業界の中でも、私たちはDXへの動き出しが早かった方だと思います。クラウドシステムにこだわり、様々な業務のDXを進めてきました。組織を強くするという観点からは、海外に製造をシフトした際、人材交流をしてみたりして、よくある育成手法を試してみたこともあったのですが、あまり効果が出なかったという経験もありました。私たちのような規模の会社の場合、従業員が働く環境をデジタル化し、業務を標準化していく方がスタッフも早く仕事を学び、投資としても、教育としても効果的だと感じています。
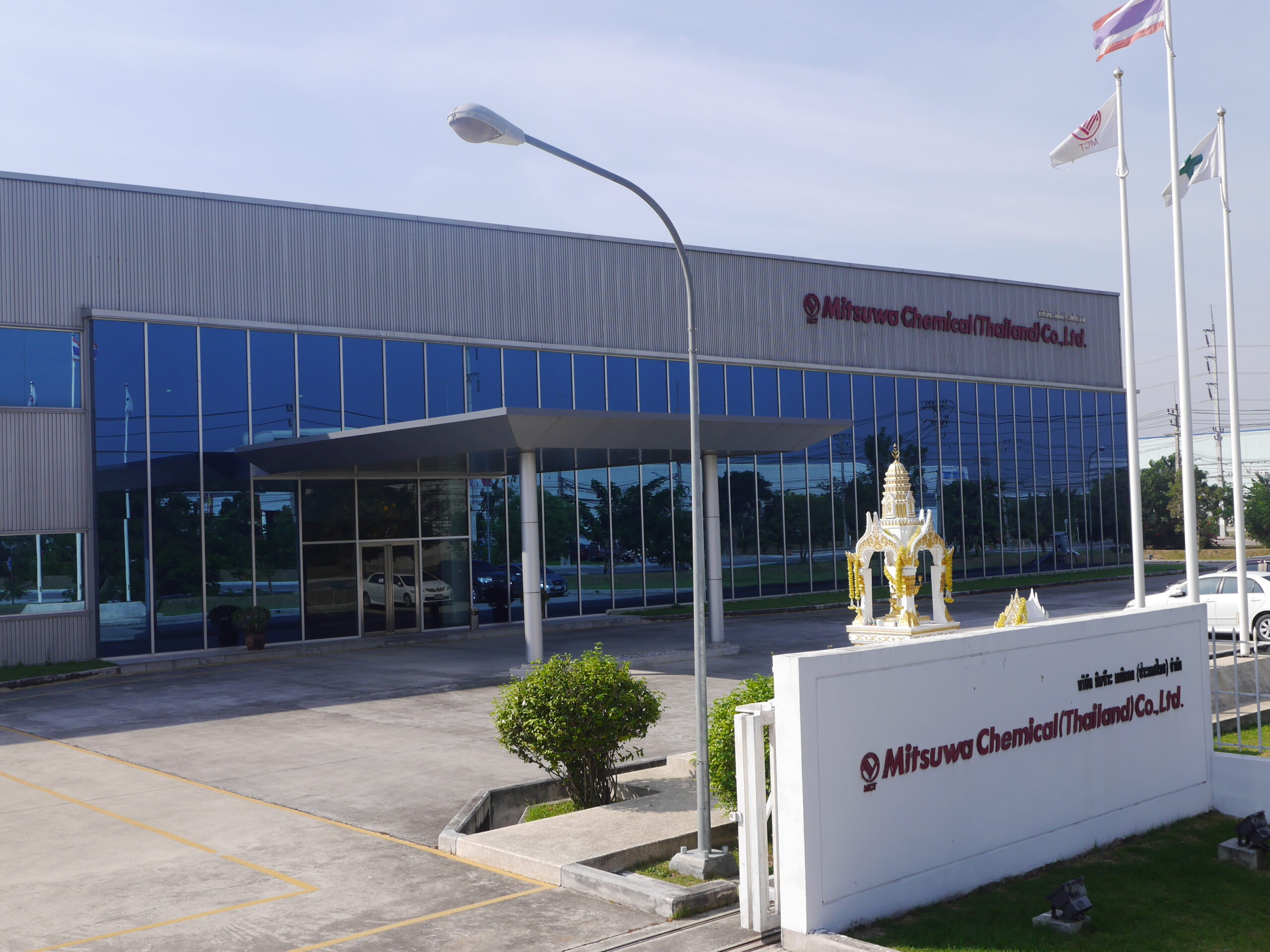
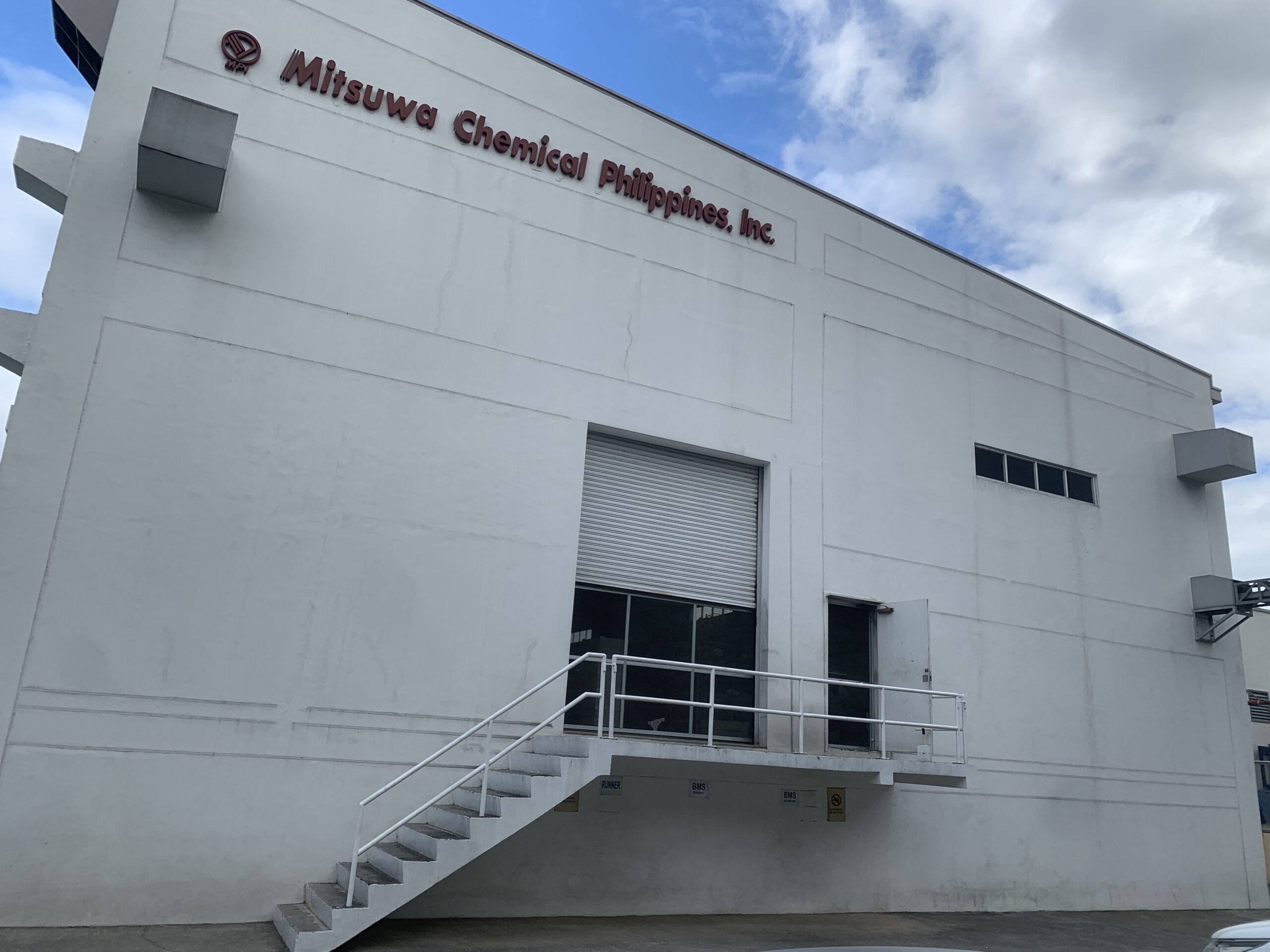
設備も運用も規格を定め、業務を標準化していく
この様な背景から、業務標準化は徹底して行っています。例えば、成形機など製造機械も出来るだけ同じものを使っています。朝のラジオ体操から始まる日々のスケジュールもほぼ同じです。各国の文化や法律による微調整が必要なこともありますが、基本的なフレームワークは全て一緒です。こうすることで、拠点間で人材が移動しても、すぐに同じやり方で業務に取り組むことが出来ます。
システム面では、クラウドサービス活用によるDXを通して、標準化を10年以上前から推進しています。自社サーバーを管理するのも、そのためのIT人材を確保するのも大変ですし、積極的にクラウドサービスを取り入れてきました。フィリピンとタイの2拠点はシステム的に統合していて、全体で「Google Workspace」、プロジェクト管理ツール「Backlog」、名刺管理・営業DXサービス「Sansan」、人事管理システム「HRBrain」、クラウド管理クラウド「ジョーシス」、受発注・生産在庫管理「ATOMSQUBE」などを活用しています。拠点間で異なるツールを使えば、カレンダーやファイル共有も困難になりますから、非効率でコミュニケーションの壁が生まれてしまいます。
こういった業務標準化の成功例ですが、業務の進捗が一目でわかる開発管理システム(Backlog)はかなり役に立っています。開発部署の上長が業務の進捗を一目で把握できるので、朝礼時の業務確認の効率が格段に上がりました。逆に苦戦している点ですが、会計システム・給与システムはタイとフィリピンにおいて基準が異なるため、システムそのものの統合が難しく、また受発注システムからのデータ移行の困難や、国ごとの会計・商慣習にあわせた帳票フォーマットも苦労している、といった事例もあります。生産計画DXについては、法律や会計基準の差異による影響を受けにくい領域なので、その心配はないですね。
現場から「我々の工場はこうやりたい」という提案は、もちろんあります。無理にグローバルで一律化するのが、必ずしも良いわけではないでしょう。ローカルに合わせた細部の調整はありますが、ただ基盤は一貫性を保つことが大事です。なぜなら、ローカルで構築してしまうとプロセスも成果もバラバラになり、良し悪しの比較や検証が難しくなるからです。同じ基準を持つことで、各工場やチームのどのやり方が最適か、客観的に評価しやすくなります。
業務標準化は、単に現場レベルの効率性を向上させるだけでなく、経営判断のしやすさにつながります。
SaaS活用で業務フローも改善。成果を出す手段としてのDX
システム導入時には、基本個別カスタマイズは不要と考えてます。そもそもGoogleなどはカスタマイズ不可能です。システム会社には、いっそ「カスタマイズできない」と明言してほしいくらいです(笑)もちろん、欲しい機能がすべて実装されるわけではありませんが、SaaSの最大の利点は、世の中のベストプラクティスを活用できることです。また、もし個別カスタマイズを優先してスクラッチでシステム投資をしていくと、SaaSの恩恵であるアップデートされ常に最新機能を使える利点を失います。もしSaaS製品を使いこなせない、適応できない理由があるとすれば、それは私たちに問題がある。既存のやり方に固執せず、業界標準やベストプラクティスに合わせるべきだと考えています。
SaaSサービスはまずは使ってみて、その良さを体感することが大切です。ただ現実問題として、新しいツールを導入するには既存の業務を変更することが必要で、これは担当者にとっては大きな負担です。また、慣れるまでに時間がかかるのも理解しています。これらは避けられない難しさでもあるので、頑張ってやりきるしかない部分です。トライアンドエラーするなら早い方がいいので、私自身は「やるなら、すぐやろうよ」とはっぱをかけています。使ってみれば、何を改善すべきかも見えてきますし、新しいツールの価値も見えてきます。
結局のところ、我々がやりたいのは効率的に業務をこなすことです。DXはその手段であり、効率化を実現するためには、必要に応じて業務フローを変えるべき、そのように考えています。一度SaaSサービスの導入に成功すると業務の習慣が変わりますね。最適ワークスを活用して進める生産計画DXにも、このような変化が見られることを期待しています。
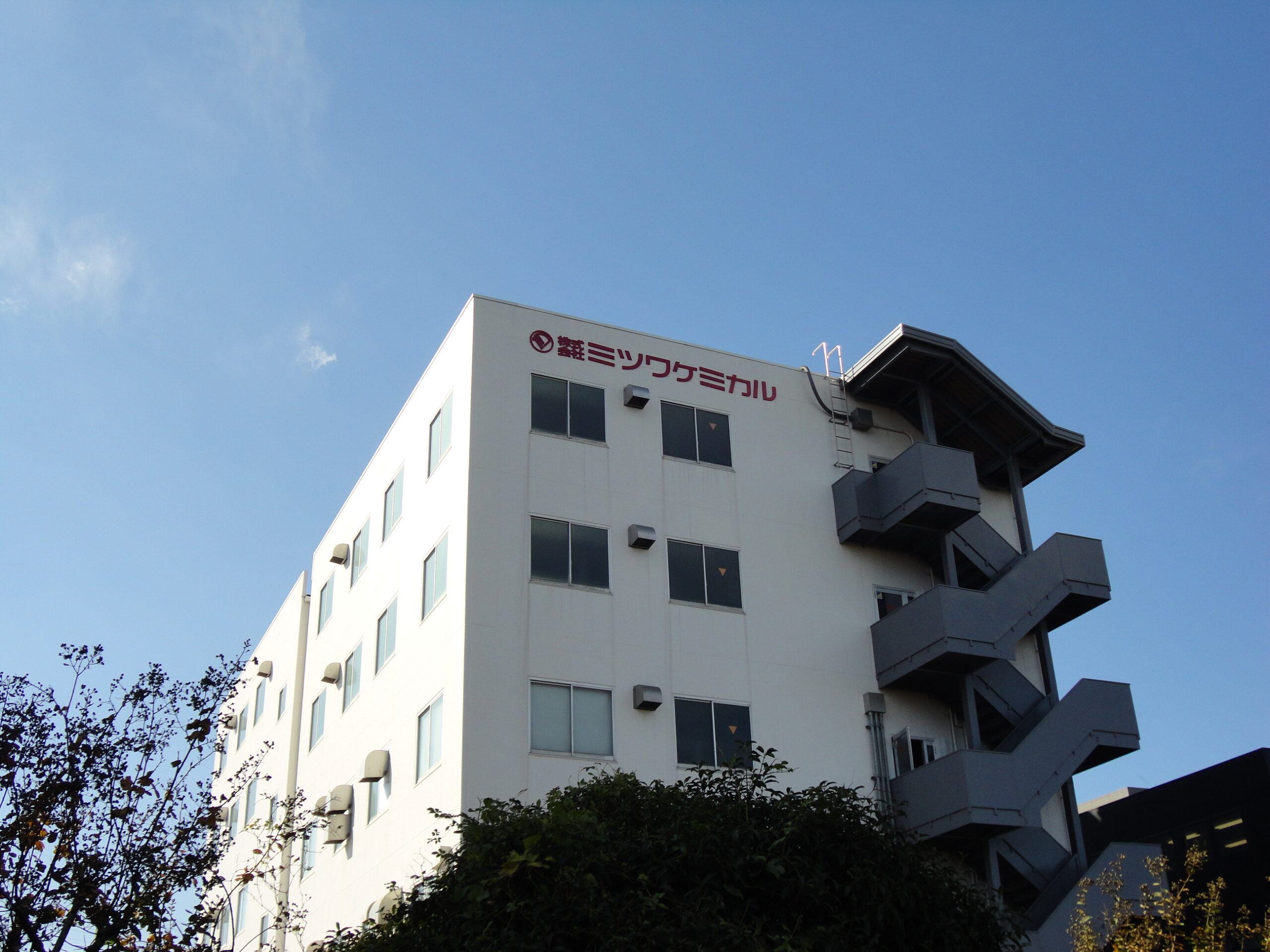